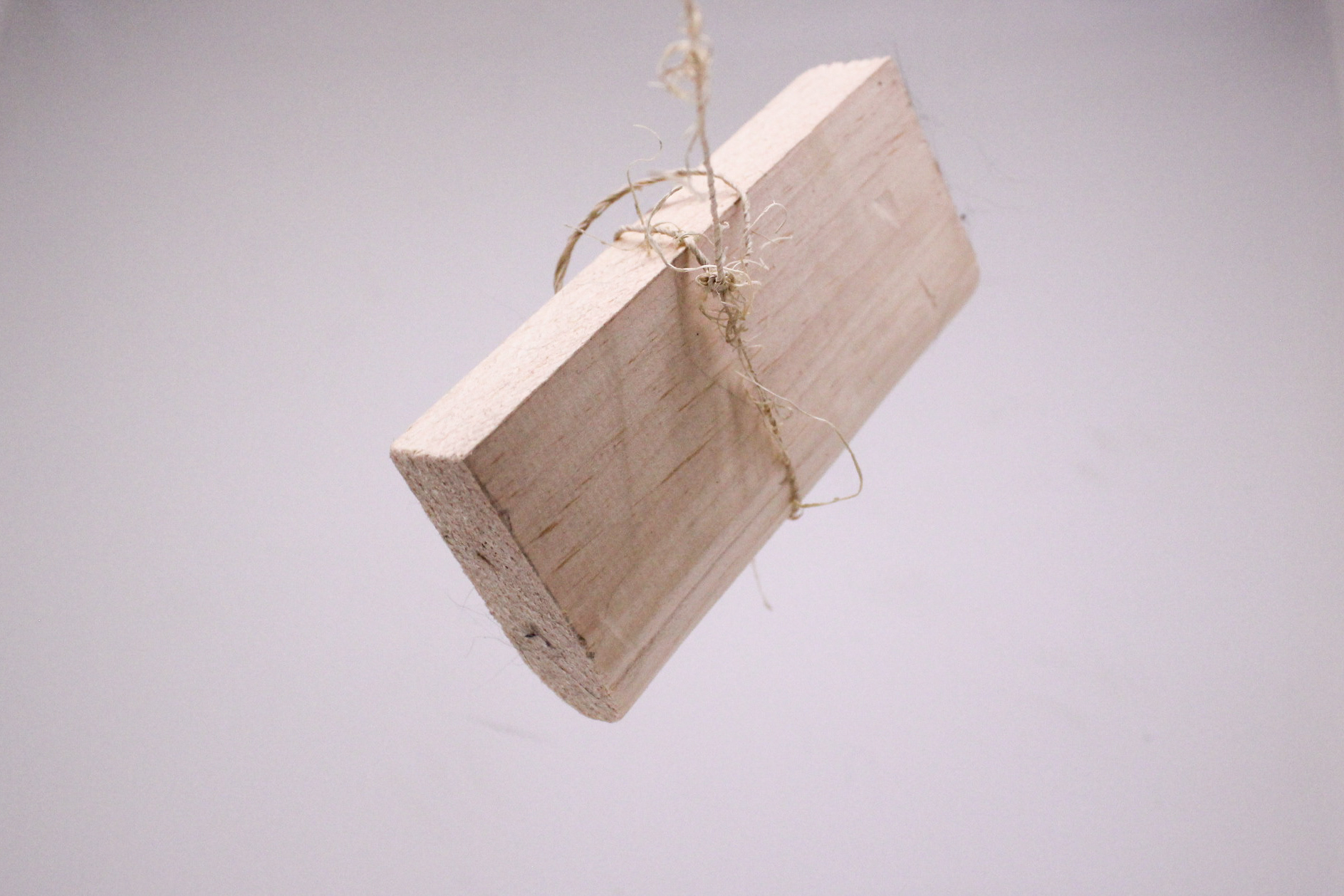
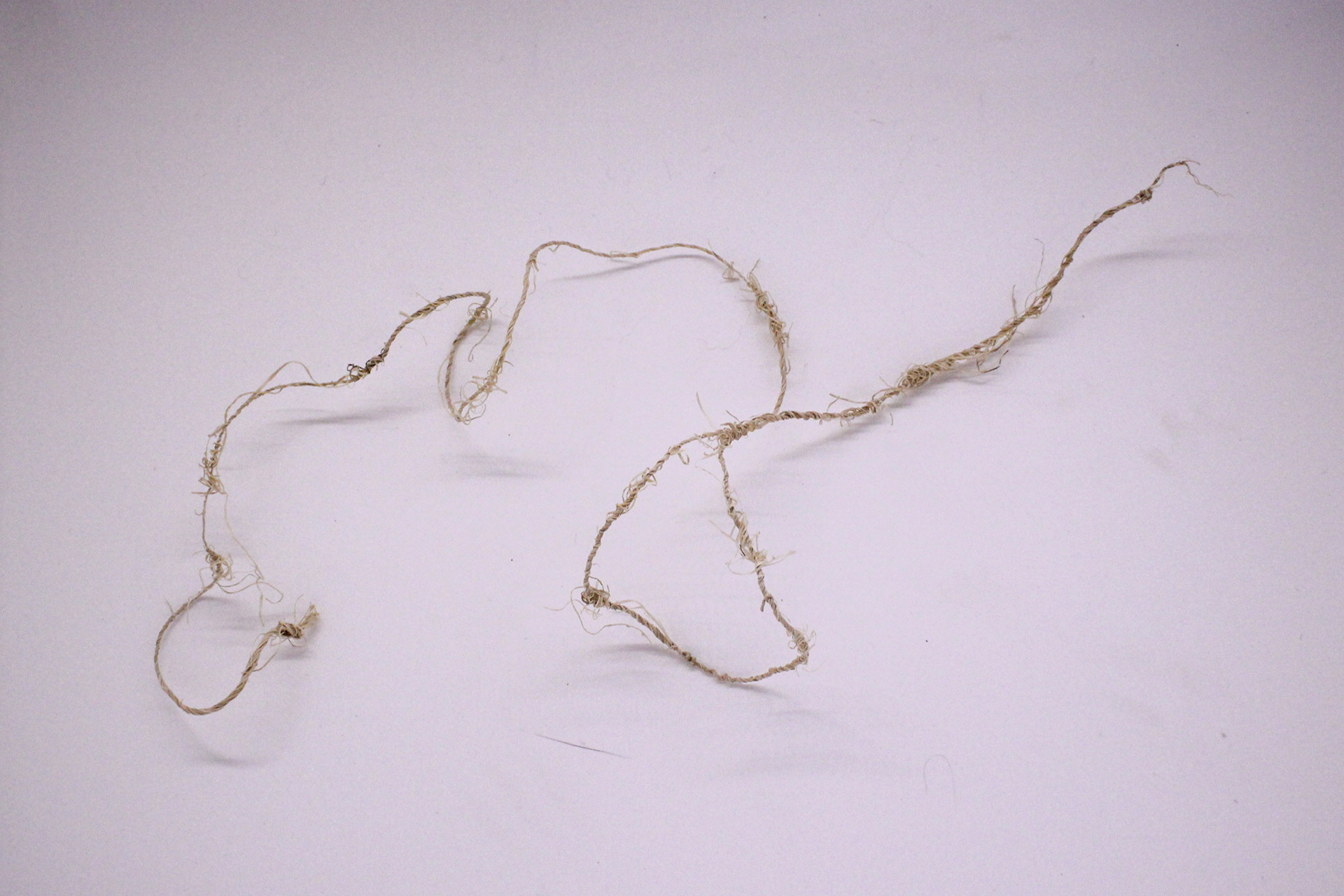
Background
My goal at the start of this project was to adapt and test preindustrial and/or modern non-industrial methods of processing flax and other fibre plants for the purpose of harvesting fibres from corn husks. My interest in this particular material was inspired by the fact that fresh corn comes with a large amount of unavoidable organic waste in the form of husks. Although municipal composting programs are becoming common, these are typically only available to residences. Restaurants and other food-service activities create a large amount of organic waste that usually goes directly to landfills. When the restaurant I cooked at ran a fresh corn special in the summer of 2019, I was struck by the sheer volume of husks being thrown away, and became interested in discovering ways to divert them as a resource.
I first experimented with this corn husks as one element of a lamp design project in fall of 2019, and have since been interested in refining my process. Using what I learned from that experience and new research into methods from historical organizations and artisan makers, I developed plans to separate and refine the corn husk fibres. Whereas my previous exploration was mainly done by hand, this project involved adapting basic tools used for processing traditional fibres (in particular flax) in order to work with corn husks.
Rather than working towards a specific idea of what I might make at the end of the process, I intended instead to reflect on the qualities of the resulting material in its existing state and (depending on the outcome) test it in any applications that seemed appropriate.

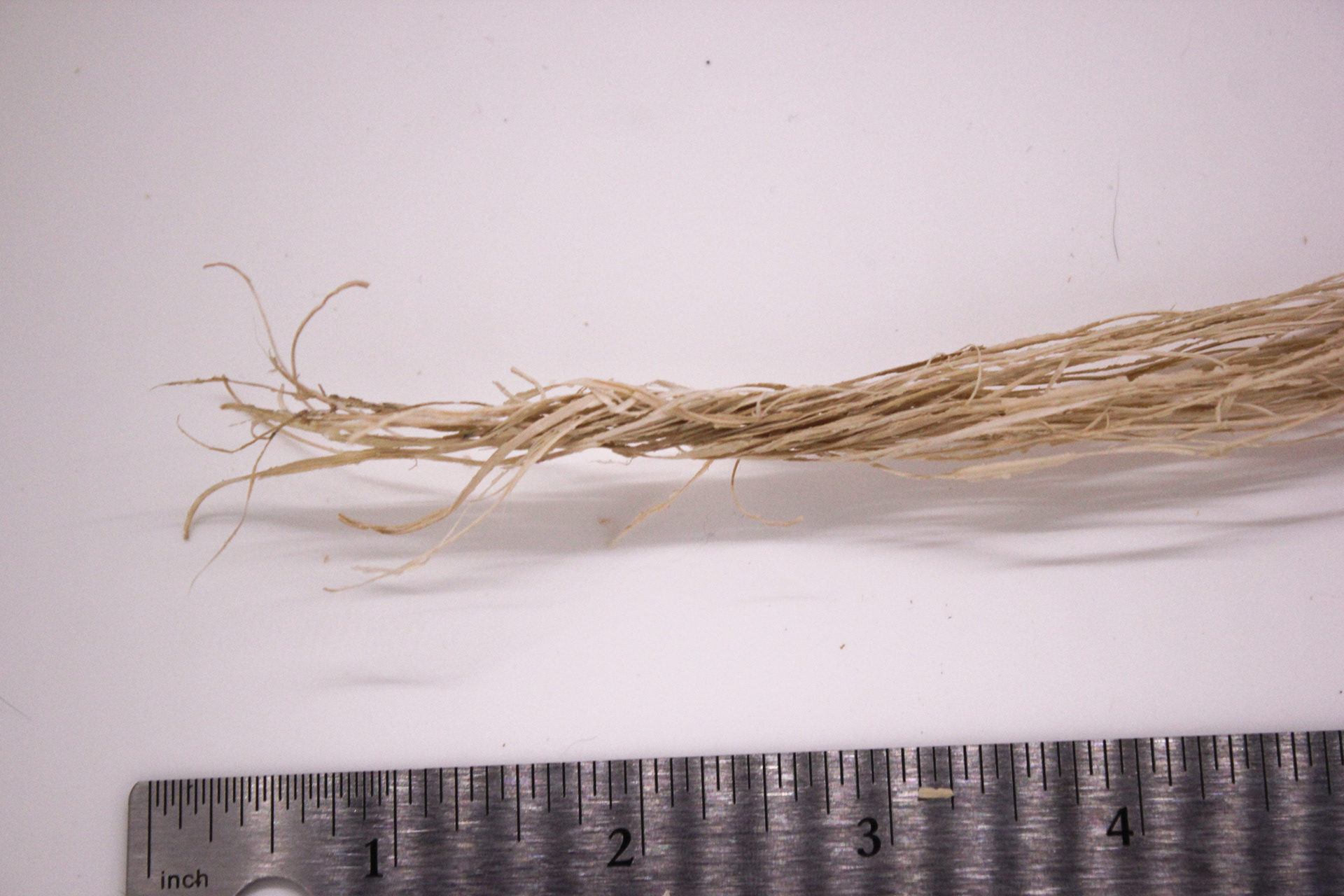
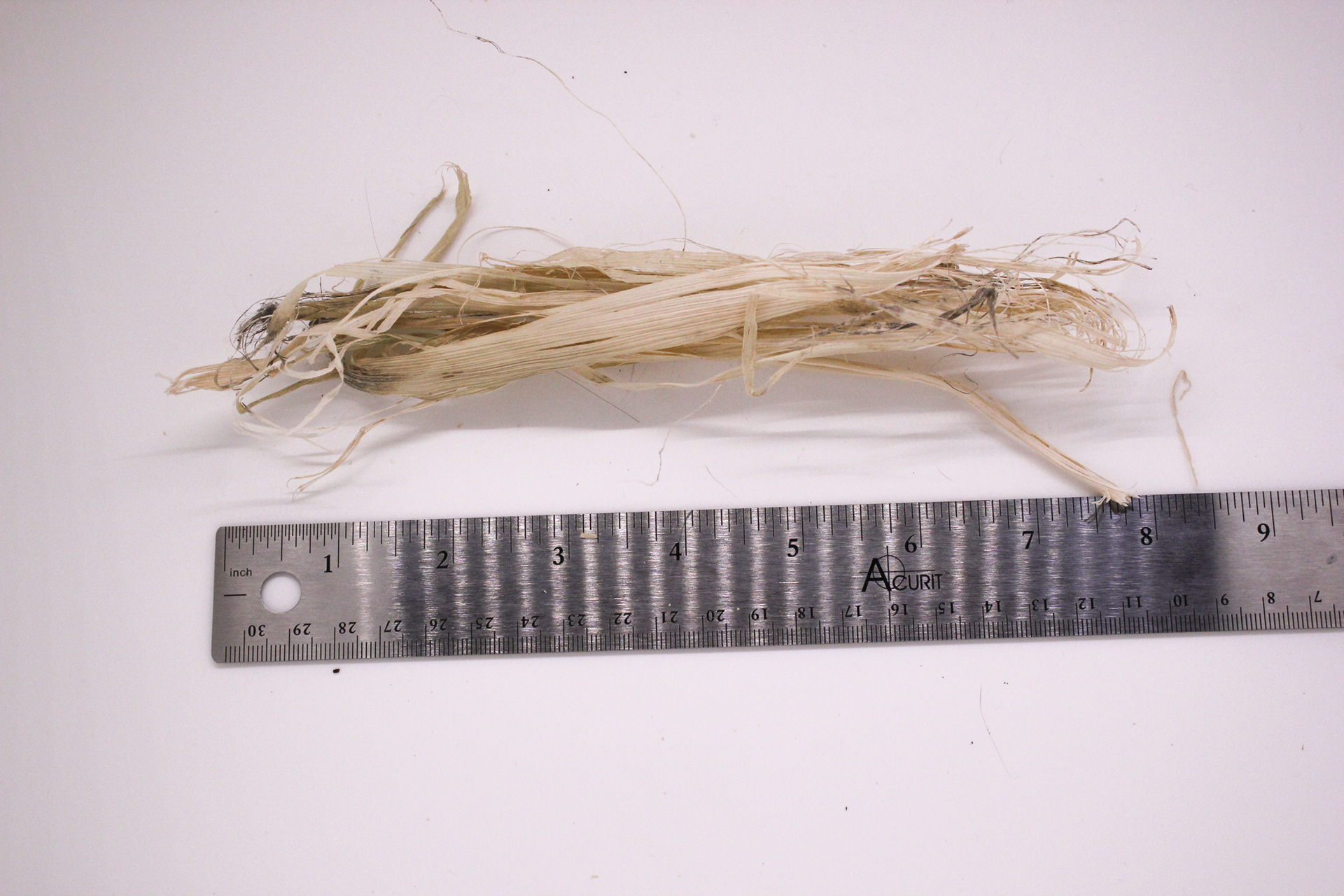
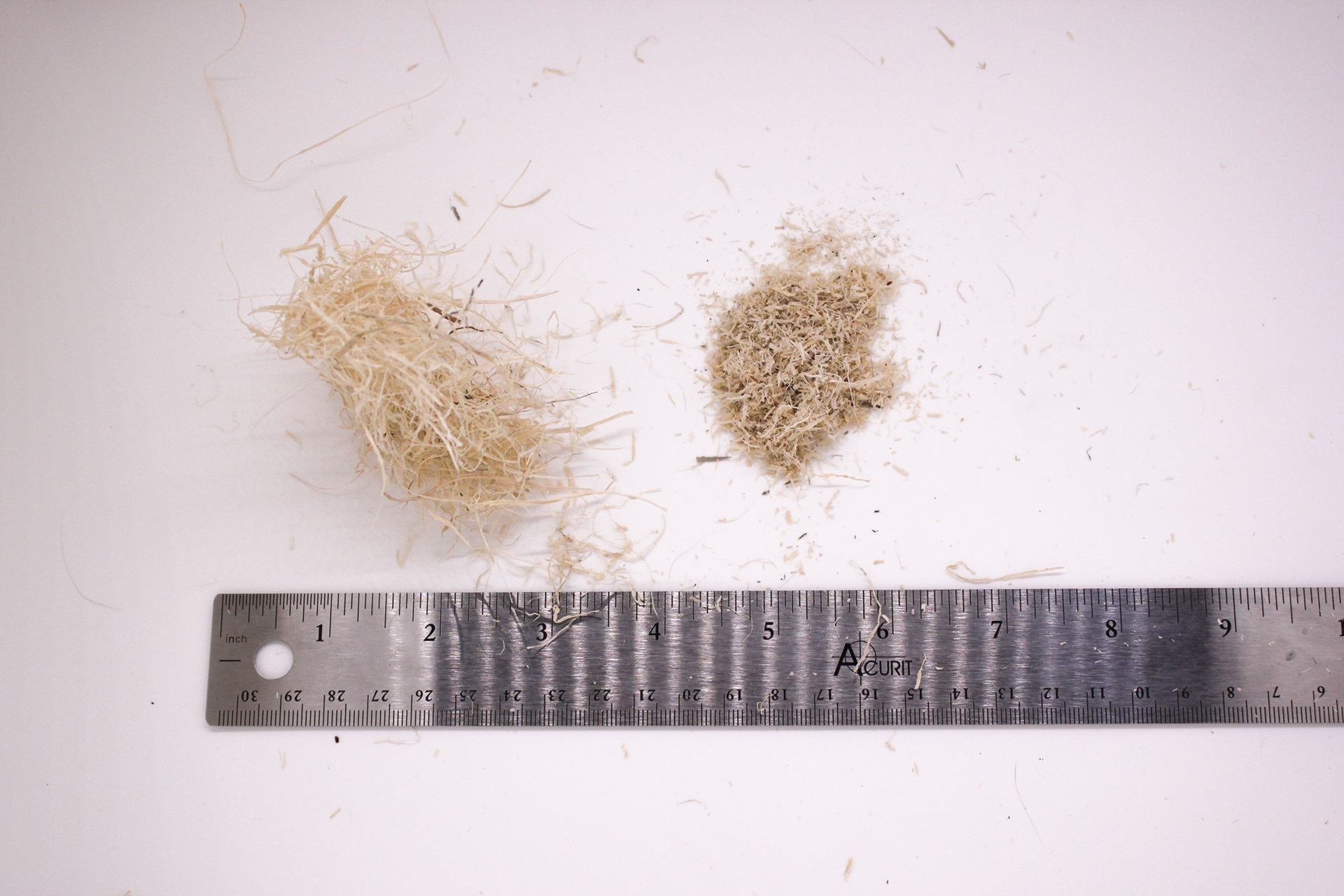
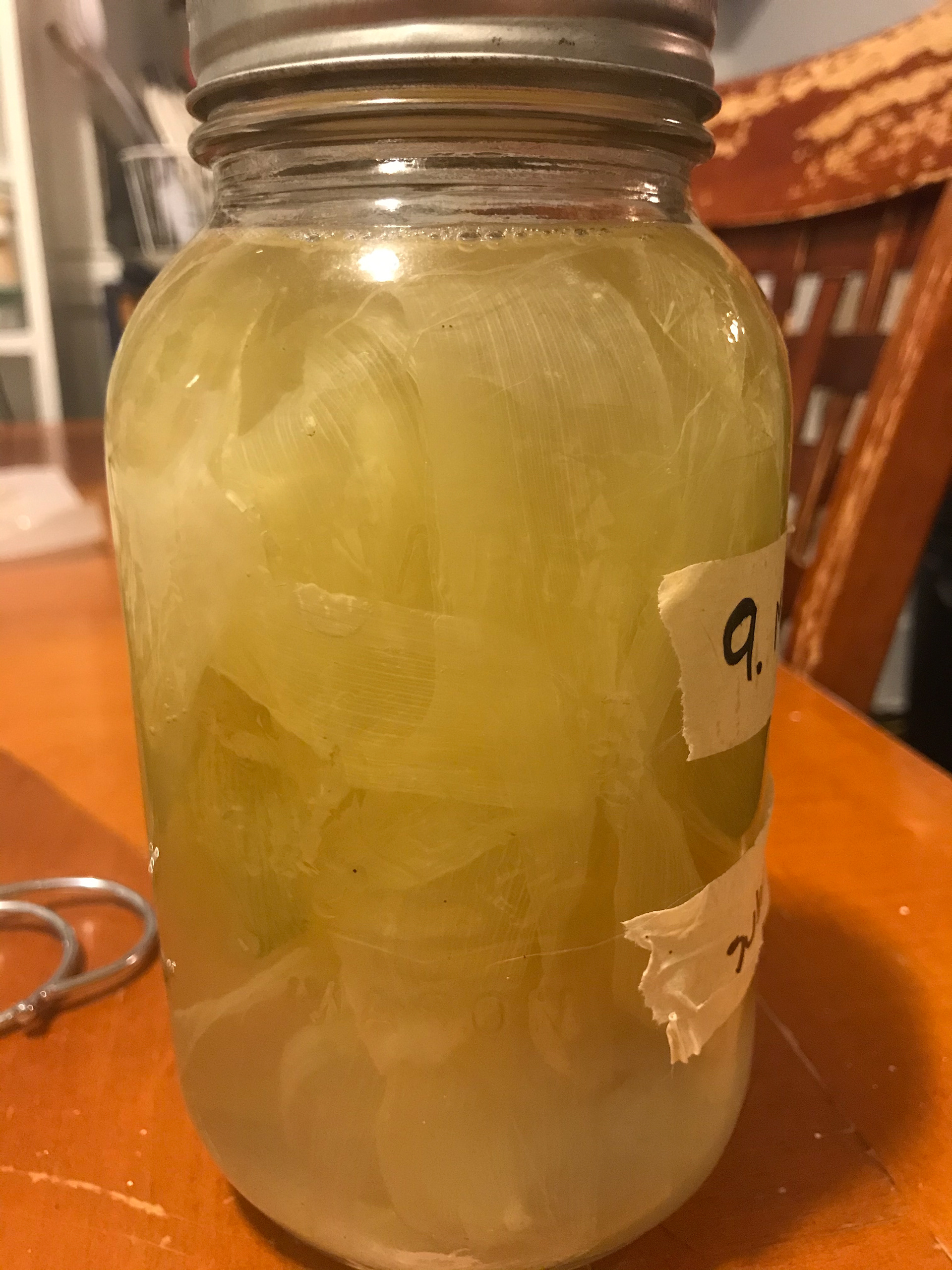
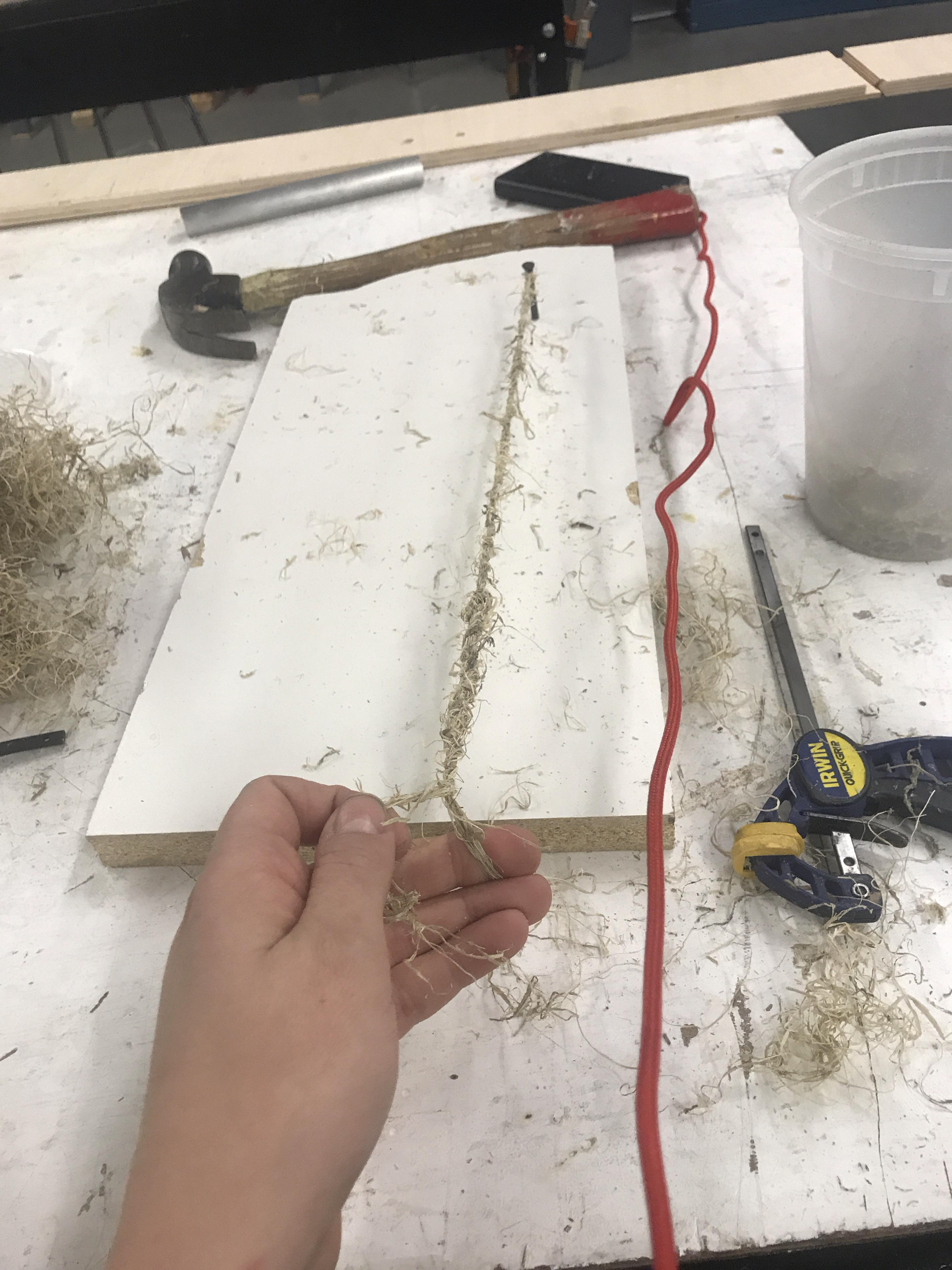
Process
I initially planned my process based on the ones described by several homesteaders, historical organizations, and folk schools—especially Homeplace Earth’s “Flax to Linen Workshop” and a series of Youtube videos by the channel attheHermitage. However, it became clear throughout the project that I would need to pay as much attention to what the material was telling me as to the established methods used for other fibres. Throughout the work I expanded my research from the methods used for processing the more common bast (stalk) fibre plants to include plants used for leaf fibres as well. Demonstrations of piña fibre processing were especially helpful (Likhang Piña: Fiber Extraction Process).
Starting Materials
I started this with two sample sets of husks: one dried, and one fresh. Each batch was taken from roughly one dozen ears of fresh corn. Because of the volume of the material, this seemed like a large amount to work with in home experiments, but as the work progressed I wished I had started with more.
Step 1: Retting
Microbial retting is a process in which fibre plants are kept either damp or submerged in water for a period of time in order to promote bacterial activity that breaks down the connective tissues between the long cellulose fibres. As I discovered in my previous work, this is an extremely effective method with corn husks. H0wever, I learned in my preliminary research for this project that I had likely over-retted my fibres in the past, which may have contributed to them being too brittle and delicate to clean properly without breaking the fibres.
For this project, I more closely followed the recommended timeline used for flax fibres. I submerged the batches of fresh and dried husks in separate containers of water for one week, checking daily to monitor the progress and to ensure the husks were still submerged.
Step 2: Washing
At the end of the retting process, I drained and rinsed the fibres. They had a strong stagnant odour, which I have since read may be helped by changing the water throughout the retting cycle (“Flax to Linen Workshop”). I washed them with a gentle biodegradable detergent until there was no unpleasant smell, which also turned out to very effectively clean away some of the connective starches that remained.
Step 3: Scraping
Although much of the connective starch was removed by retting and washing, some still remained. There was a layer that was thicker at the base of each leaf. I had initially planned to dry the husks at this point before finishing cleaning them, but I found that this starch was quite soft when wet and I could remove it with a fingernail—so, taking inspiration from the methods used for piña fibres, I decided to scrape away this starch while it was still wet.
I worked on a small plywood board that provided some grip to the fibres and absorbed the excess water well so I had a fairly clean workspace. A kitchen bench scraper was an ideal tool for this—a scraping edge that is not so sharp as to damage the fibres comfortably sized for the hand, and slightly flexible. Using these tools, I simply scraped along each side of the fibres in batches, removing the excess starch as a paste—the process was time-consuming, but resulted in much cleaner material than my previous experiments, with far more of the fibres intact.
Step 4: Drying
After scraping, I hung the fibres up to air-dry. Without the additional starch, the fibres dried within a day‚ much faster than they had in my
previous work.
previous work.
Step 5: Breaking (but not really)
Following the processes used for linen production, I made a very scaled-down, table-top adaptation of a flax brake. Traditionally this is a standing tool with a hinged rounded “blade” that is used to break up the stiff stalks so they can be further separated without damaging the fibres.
However, when I tried to use it, I found that the husks were already quite supple, and neither needed nor benefited from this treatment. This realization confirmed to me that I would need to be flexible and adaptive throughout the process, rather than feeling the need to apply traditional methods to a non-traditional material.
Step 6: Hackling/Carding
I did continue to take some cues from flax processes. The next stage would typically be hackling—essentially working the fibres through a progressively finer series of comb-like spiked tools. Because the corn fibres are much shorter than flax and other bast fibres, I decided to work with carding rather than hackling tools—these are more like brushes, and are used for cleaning and aligning shorter fibres like wool, and were recommended as a way to salvage shorter flax fibres too (“Flax to Linen Workshop”). Because my fibres were already well on their way to being separated after scraping, I was able to start with a fairly fine tooth.
Unfortunately carding tools are fairly expensive, but I was able to find used carding cloth panels. I temporarily fastened them to makeshift paddles out of scrap wood—my main concern was to keep the cloth flat for this purpose, but I do intend to make paddles with proper handles at some point when I can access the tools to do so.
I carded each batch of fibre until it was separated and aligned, although bits of leaf matter remained at this stage. This was quite a dusty process and I had to wear a mask throughout. Some of the fibres broke during this stage, so I separated and kept three separate groups of material: the long fibres, short (1-2”) fibres, and what was basically a coarse dust left over.
Step 7: Refinement
I tested multiple methods to further clean small samples of the fibres after the initial carding. On one, I tried dampening the fibres to soften the starches before carding a second time. On the second, I used a fine comb to brush out the rough bits of matter. On the third, I dampened the sample before combing. Interestingly, I found that the husks that had been retted while fresh came out best by being dry combed, while those that were retted after being dried had the best results from being damp-combed. After comparing the results of the tests, I finished the remainder of the two original groups respectively.
Step 9: Spinning
In order to build on my tests with hand-twisted twine, I decided to try spinning the fibres using a drop spindle. Unfortunately, this was my first experience using a drop-spindle so there was a steep learning curve, but I was able to successfully spin two samples using the fresh-retted fibres. One was made of pure corn fibres, and one in a 50/50 blend with wool. I finished the pure corn sample by trimming some of the loose ends that stuck out, resulting in a much cleaner texture.